Case Study: Steel and Pipe Supply Leverages xECM for xCeptional Digital Content Management
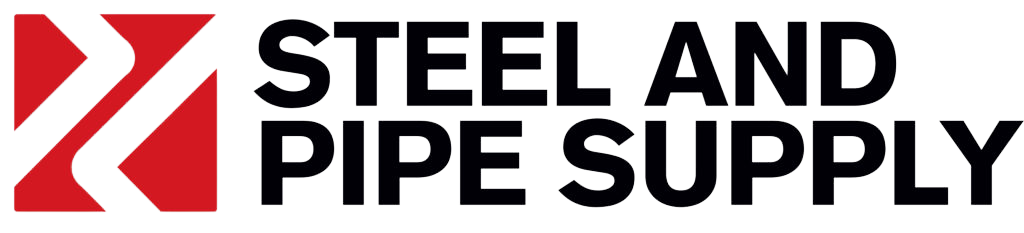
June 4, 2021
Table of Contents
About Steel and Pipe Supply
Steel Pipe and Supply’s (SPS) family of companies has built its carbon steel product, distribution and logistics businesses based on the latest coil- and value-added steel processing technology. Considered one of the largest privately held steel service centers, SPS has locations throughout the Midwest and Southern regions in the U.S. and in Mexico. The corporation’s business lines include coil processing; toll processing; value-add processing services; galvanizing; tube and specialty pipe; metallurgical testing; storage and handling; and steel distribution and logistics.
To learn how Optima and solutions from SAP and OpenText enabled Steel and Pipe Supply to achieve new levels of operational excellence, download the full case study today.
In the steel industry, smart manufacturing, robotics, analytics, and enterprise resource management are forcing digital transformation and innovation. For more than 80 years, Steel and Pipe Supply (SPS) has faithfully served customers with a diverse assortment of carbon steel products, deep inventories, a strong supply chain, and value-added processing. With numerous business lines and complex logistics, their documentation for manufacturing and distribution are an essential component of their business success. They needed to update their systems to leverage the institutional knowledge and experience that powers their competitive edge.
The Challenge
Two key documents, Mill Test Reports (MTRs) and Proof of Deliveries (PODs), are critical to the quality, risk management, and traceability processes SPS offers. These documents can make or break loyal customer-supplier relationships. The SPS IT team realized that to best serve their customers and improve efficiencies in the business, they needed to upgrade their content management system to a more powerful, modern, and adaptable solution.
The Obstacles
Shifting from their legacy system to new integrated systems presented a number of hurdles:
- Employees accessed MTRs and PODs from eight different physical sites
- MTRs and PODs were stored in 12 different locations and were plagued by missing information and errors
- No internal or external standardization of MTR and POD data and documentation formats
- All MTR and POD data lived on a wholly separate, antiquated legacy system
- System integration issues and labor-intensive document processing was causing delays and frustrations internally and with customers
The Solution
The content management experts at Optima considered Steel and Pipe Supply’s short- and long-term business goals, architecture, and integration requirements to ultimately choose SAP Extended ECM by OpenText as the best solution. Working in lock step, SPS and Optima re-architected and optimized complex workflows to take advantage of system capability and eliminate their reliance on outdated processes and systems.
The Results
- Decommissioned multiple homegrown applications to store Material Test Reports and Proof of Deliveries
- Eliminated costly custom interface maintenance
- Improved process efficiency by linking PODs into SAP Deliveries via Barcodes, avoiding manual entries
- Increased performance in Quality Control and Logistics Efficiency
- Improved Customer Service by creating ability to immediately display Test Reports and POD via Hybris
- Ensured electronically stored documents were easily available for retrieval via SAP or Web Interface
- Decreased customer returns and complaints